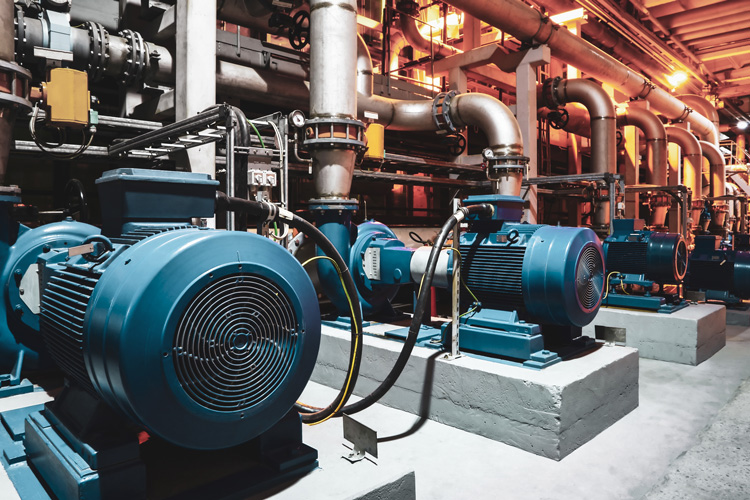
监测安装在电机、泵和其他工厂平衡旋转资产内的轴承的状况,通常由训练有素的专业振动分析师完成,并辅以复杂的软件和便携式数据收集BETVICTOR体育官网器。使用基于路线的技术,分析师通常会在工厂内沿着预定的路径行走,在每台机器前停下来,并使用加速度计和上述收集器读取振动数据。路由完成后,收集的数据被上传到主机上,通常由更有经验的分析师审查和分析数据,以确定是否有任何机器故障。这种状态监测方法产生大量数据,需要(通常是几个)人类专家操作,有时间限制,如果不一致地执行,很容易遗漏重要的机器故障。值得注意的是,可以在没有问题的机器上花费大量时间。当然,额外的安全考虑,例如让人员暴露在旋转机器的潜在危险中,也在发挥作用。
由于技术的进步,特别是工业物联网(IIoT)的出现,状态监测现在可以通过使用无线、电池供电的振动传感器实现自动化,这些传感器永久安装在工厂资产平衡上。这些系统使用基于云的平台进行数据存储,以及人工智能(AI)或机器学习算法来建立振动报警限制和机器故障诊断。这种自动化将振动专家从常规的数据分析中解放出来,使他们能够专注于更有问题的、更引人注目的资产。
发现机器故障:典型场景
一位振动分析师花了大半天时间在工厂的多台机器上读取振动读数,然后回到办公室检查数据,他注意到分析软件显示,离心泵从动端轴承振动很大。振动在径向和轴向都很高,但在轴向不高。对振动波形进行快速傅里叶变换(FFT)频谱分析表明,在机器的1倍运行速度下存在一些振动,但远低于警报限制。但是一些高振动峰值出现在非同步(与1倍运行速度不协调)频率上。分析人员根据经验知道,这可能是轴承故障发展的迹象,但需要额外的分析来确认这一点。
在工厂的计算机化维护管理系统(CMMS)中查找泵的轴承部件编号,然后分析人员在分析软件中调出轴承的特征故障频率——基本训练训练频率(FTF)、球旋转频率(BSF)、外球通过频率(BPFO)和内球通过频率(BPFI)。分析师指出,特征BPFO在FFT中接近振动峰值。此外,在振动峰值的两倍频率(2X BPFO)处存在谐波。根据经验,分析人员知道这是确认轴承的外圈有缺陷。未来几天的进一步测量将确认轴承故障的严重程度,以及更换轴承的时间。分析师建议的纠正措施应包括订购新轴承和安排关闭泵以更换轴承的时间。
这个场景是否满足状态监控程序的目标?是的。分析人员能够及早发现轴承问题,采取纠正措施解决问题,从而避免意外停机。
但在这种情况下,有几件事需要注意:
- 操作此系统至少需要一名训练有素的振动分析人员。
- 整个过程是人工执行的,是劳动密集型的。
- 振动数据通过便携式数据收集器和工厂的网络基础设施本地存储。
- 目前尚不清楚震动警报限制是在哪里或如何建立的。
- 机器故障诊断是依靠分析人员的技能和经验手动确定的。
- 确认故障的严重程度需要集中注意机器,包括在预定常规测量路线之外的重复每日测量。
- 虽然没有提及,但多久进行一次测量?一个月一次?如果读数更频繁一些,机器故障是否能更早发现?
自动化状态监控
无线状态监测系统包括在工厂的旋转设备上部署电池供电的无线振动传感器。这些传感器与网关通信,网关又通过蜂窝网络连接到互联网。来自传感器的数据被发送到云端,在那里复杂的分析处理信息。然后,用户将通过PC桌面上的基于web的仪表板或手机应用程序的推送通知收到机器故障的通知。通过无线、基于工业物联网的系统,传统状态监测系统的许多方面都可以实现自动化,能够全天候、无间断地收集数据。
需要什么专业知识?
简而言之:用户不必是训练有素的振动分析师来操作无线状态监测系统。需要基本的机械知识和振动传感器安装在机器上的最佳位置。一旦安装了传感器,系统就会在后台运行,监控工厂的机器。
这样可以节省振动分析人员的时间,使他们能够专注于有问题的机器。在基于路由的程序中,分析人员花费大量时间在正常的机器上读取数据。这是因为所有的机器都必须定期检查,因为不能对机器的状况做出任何假设。使用无线系统,被监控机器的状态在任何给定的时间都是已知的。这允许分析人员将注意力集中在标记有错误的机器上。
数据在哪里,如何保护?
在传统的状态监测系统中,振动数据首先在便携式设备中收集,并在收集路径的末端上传到主机。这意味着系统用户必须提供必要的计算机基础设施,这可能需要安装复杂的服务器并涉及公司信息技术(IT)人员。在任何情况下,在任何给定的时间,数据从便携式设备传播到公司网络。由于数据通常是手动移动的,因此数据丢失的风险——从便携式设备的物理损坏到网络安全威胁导致的公司网络故障——成为一个严重的问题。
通过基于iiot的状态监控方法,无线系统不需要本地服务器或本地主机。数据也不是分散在多个设备上。振动数据在传感器中测量并传输到网关,通过蜂窝网络定期上传到基于云的平台。数据在云中存储、处理和管理。最终用户只需要一个所谓的“瘦客户端”设备——比如网络浏览器、平板电脑或手机应用程序——就可以查看数据。
关于告警限制和故障诊断?
适当的振动警报限制不仅可以保护机器,还可以让分析人员优先考虑有问题的机器。因此,设置切合实际的报警阈值是很重要的。
但是警报阈值是如何设置的呢?用户可以从国际标准化组织(ISO) 10816推荐的警报级别开始,但该标准的机器分类通常不适合所讨论的机器,并且会产生不切实际的警报级别(过高或过低)。那么机器制造商的推荐水平呢?通常这些都没有考虑到实际的操作现实,这尤其适用于较老的设备。因此,警报阈值往往由经验丰富的分析师设置,尽管这可能需要大量的试验和错误才能准确地拨入。
相比之下,基于工业物联网的无线系统采用人工智能,结合机器学习算法来自动设置报警阈值。这意味着在机器实际运行时,系统会在训练阶段学习机器的行为。如果机器被修理或大修,从而改变了操作行为,用户可以简单地重新开始训练阶段。
在传统系统中,训练有素的专业振动分析人员可以诊断机器故障——假设提供了足够的时间和适当的数据来进行分析。然而,在无线系统中,机器故障诊断是自动的,因为每次测量都在云中处理振动数据。滚动轴承故障诊断可能是人工智能应用的最好例子,特别是在早期检测故障方面。与每个轴承零件号相对应的是轴承制造商提供的特征故障频率。当无线系统分析振动波形的频谱时,它将寻找与这些特征频率匹配的振动峰值。虽然人类分析师也可以这样做,但基于工业物联网的无线系统会自动执行这种分析。
数据的粒度
如前所述,传统的基于路线的状态监测系统主要由分析人员沿着预先计划的路线对机器进行测量组成。但是分析人员多长时间重新启动路由并返回到同一台机器?在同一台机器上的同一位置上进行振动读数的频率是多少?更频繁的读取将产生更平滑的数据粒度,而不频繁的读取将产生粗糙的粒度。尽管许多分析师渴望重复这一路线,每个月在同一台机器上进行读数,但经验告诉我们,这种情况并不总是发生。也许分析师被某个特殊的项目拉走了,或者出于某种原因,决定在本月跳过这条路线。如前所述,如果一台机器被标记为有问题,那么这台机器所需的额外时间和注意力可能会使分析人员脱离他们的常规路由计划。任何导致测量遗漏的因素都会在数据中产生盲点。同时,在两次测量之间机器发生了什么?如果分析人员知道机器上的数据可能几个月后才会再次采集,那么他现在能确定机器故障吗?
永久安装无线振动传感器的系统每天多次读取数据,消除了数据盲点。这导致了效率的提高,因为许多机器运行良好,不需要分析人员的注意。当系统确实标记出有故障的机器时,分析人员可以
把注意力集中在那台设备上,要知道工厂里的其他机器都在被监控。
技术的进步,包括基于云的工业物联网设备的发展,使基于振动的无线状态监测解决方案比传统的基于路由的系统更具优势。由于不需要专业的振动分析人员来操作系统,他们的时间被腾出来专注于有问题的机器。
此外,IIoT无线系统是基于云的,这最大限度地降低了数据丢失的风险,并消除了终端用户提供计算机基础设施来存储和处理振动数据的需求。此外,云平台内置的分析功能可以实现自动振动报警阈值和机器故障诊断。
但无线系统最大的优势可能是永久安装的传感器,每天读取数据。这与基于路由的系统形成对比,后者可能会在数据中留下盲点,并使分析师在两次测量之间猜测机器的状况。