在售后市场业务中,零件复制是不够的。精密工程与最新技术相结合是制造高质量零件的必要条件。美国中西部一家发电厂的主锅炉给水泵建于1967年,采用砂型铸造和木制模式,现在被认为是过时的技术。尽管泵每6到8年进行一次翻新,但BETVICTOR体育官网泵的性能仍然很低,并且存在振动问题。
这家工程和维修服务公司利用其所有资源,包括铸造模拟、3d模型、最新铸造技术和大量的工程数据,制造了一个完整的元件,在泵测试实验室批准程序(PTLA)认证的测试实验室进行了复杂的测试,并在短短12周内将泵重新投入运行。BETVICTOR体育官网
这个项目包括制造一个完整的第一阶段双蜗壳和潜在缺陷的描述。
泵遭受持续振动问题,这是由叶片频率的压力脉动引起的。为了提高振动水平,需要进行水力分析和重新设计,以开发新的改进设计。
这个项目分为两篇文章。首先是双蜗壳的制造,其次是新型叶轮的设计。
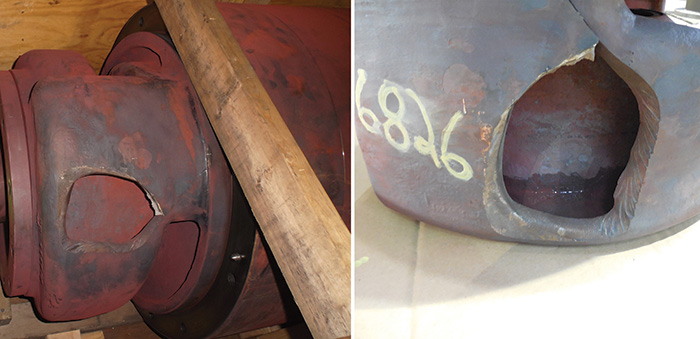
第一级双蜗壳是一种复杂的铸件,由于设计不良,在使用过程中发生了故障。
工程和维修服务公司通过使用复杂的工程和3d建模,以及模拟软件和3d砂打印对铸件进行了重新设计。
此外,该公司通过重新设计第一级双吸叶轮,确定了提高泵性能的机会。为了提高叶片通过频率,对第一级双吸叶轮进行了重新设计,采用了交错叶片和分裂叶片。
该公司的售后服务能力为这种高能锅炉给水泵提供了全新的替代元件,并重新设计了铸件,以消除铸件设计中原有的潜在缺陷。
该公司提供了复杂的水力工程改进,以增加新制造元件的平均维修间隔时间(MTBR)。
背景
当泵壳的预期寿命没有达到预期时,最终用户遇到了一个问题。由于泵的性能恶化,表现为振动加剧,因此停止使用。第一级双吸蜗壳失效。从焊接芯塞与蜗壳铸件的交界面开始,在蜗壳上产生了裂纹。
在铸造厂,图像是用清晰的内径瞄准镜拍摄的,并“按收到的”进行处理。结果表明:蜗壳交叉壁面有烧砂,交叉圆角处有轻微闪光,清洁通道表面光洁度可接受。对泵进行逆向工程,发现了原铸件的一个潜在缺陷。
故障的根本原因
传统的铸造工具有时需要支撑方法来保持芯在模具内的位置。岩心是由粘合剂粘合在一起的砂粒,这些砂粒被装入工具中,形成特定的几何形状。泵部件的核心构成了大多数内部几何形状。
挑战在于一旦金属开始填充模具,如何确保芯的安全。在铸造厂中,当需要在模具内支撑芯时,使用链链是一种常用的方法。膜片是一种小型金属隔片,与铸件壁厚相匹配,可以最大限度地减少岩心的移位或抬升。负面影响是,在清洗过程中,它们通常需要挖掘和焊接。
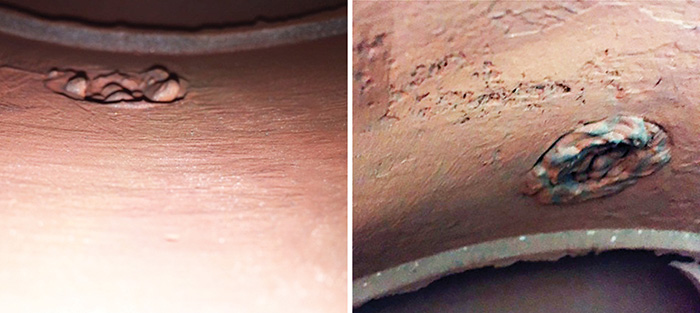
晶片通常由不同于被浇铸金属的冶金材料组成,如果留在原地,可能会产生一个薄弱的区域。图2显示了用于小链或岩心清砂桥塞的区域,这些区域经过挖掘和焊接。
工程师们通过使用3d技术消除了浇筑过程中对小环的需求,该技术允许在混合设计中制造核心,将其锁定在模具内。采用该方法,使壁厚平均化,芯移最小化,焊接量最小化。用镗孔镜检查蜗壳区域并进行适当清洗。
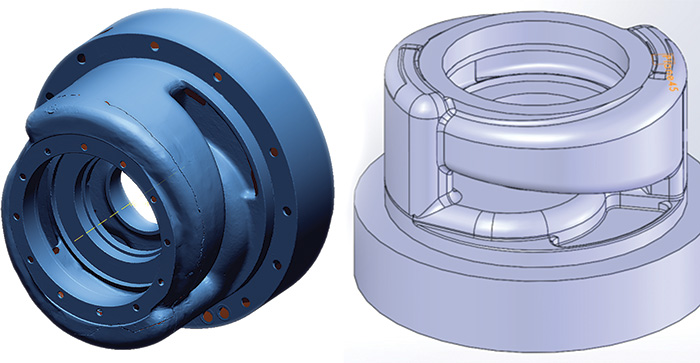
铸造缺陷
在蜗壳交叉区域,工程和维修服务公司注意到两侧都有大量闪光。这是由两个岩心连接在一起的岩心提升产生的。虽然3d打印方法并不能消除对分离岩心的需求,但它允许工程和维修服务公司将岩心分离到可以进行研磨的区域。3d打印的岩芯在x、y和z轴上的尺寸精度为0.005-0.20英寸。这给了工程师在模具制造过程中精确的芯丝。
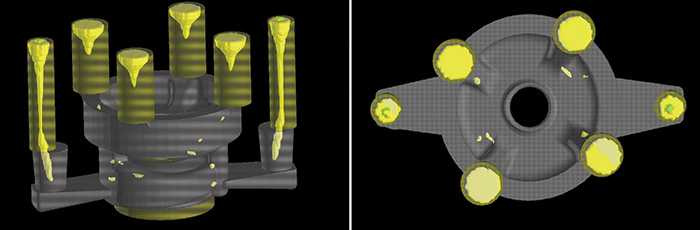
CFD凝固分析
对原材料的初步分析确定了关注的区域,以帮助指导立管模式的设计,并突出了入口的首选区域。立管是由放热套管隔热的圆柱形管,一旦充满液态金属就会产生热量。
它们通常被放置在“进料区”,这是在金属凝固过程中可能导致收缩缺陷的区域。
立管的功能是保持其金属比其进料区内的金属温度更高,以指导其内部任何可能的缺陷。浇口是浇注过程中金属进入铸件主体的地方。理想情况下,它们位于铸件的底部,以尽量减少金属内部的速度或湍流。
初始材料密度
通过增加立管和冷却器来解决两个主要的进料区域,以帮助指导金属的凝固。立管的作用是将固化杂质从母材中分离出来。
当液态金属进入模具时,不能由立管支撑的区域应该安装冷冻机来冷却较重的部分。
冷却器是牢固地放置在砂型中的固体金属片,在填充时帮助冷却金属。两种进料方法的结合使工程和维修服务公司能够生产出缺陷最小的优质产品。
最终CFD分析:极端条件
该软件包允许设计人员在最佳和极端条件下查看浇注条件。工程师将浇注温度、浇注时间、大气条件和模具材料等最佳条件输入系统。CFD软件的工作理解是,这是浇注合金时的最佳状态,范围从0-1,其中0为最佳,1为极端。这个过程评估铸造在0.9为最佳,0.999为极端。有了这些信息,工程师们设计了浇注和冒口系统,以应对浇注合金时最极端的条件。
这些迹象表明,在最坏的情况下,预测的收缩。这是最小的,可以在粗加工阶段解决。即使在极端条件下,这些预测的收缩区域也可能不存在。这是一个已被证明是准确的理论计算。然后在RT过程中对这些区域进行评估。
最终CFD分析:最佳条件
这是一个类似的分析,但在最佳条件下。所有的标志都在提升管中,铸造主体无缺陷。工程和维修服务公司为铸造厂提供了每个铸件的浇注数据表,然后满足这些规格。
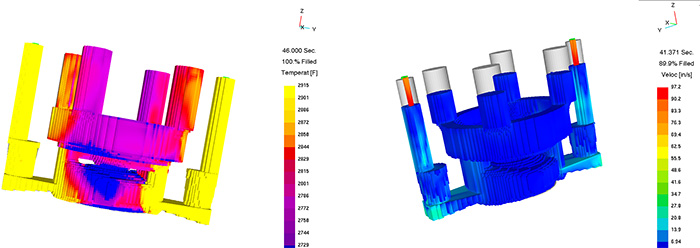
温度梯度分析
在研究金属的流动时,必须找到一种平衡,使金属在凝固过程开始之前足够快地进入模具以填充模具。与此同时,它必须尽量减少湍流。在这种情况下,主要关注的是将立管放置在温度保持最长的地方。工程和维修服务公司在浇注过程中使用双浇口方法将金属均匀地引入两侧。由于进料从两个方向运行,这可以快速馈送关键几何区域,并将湍流降至最低。
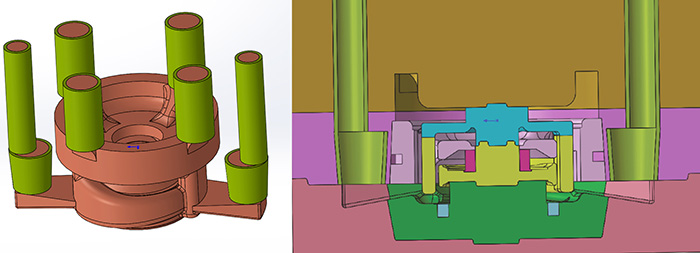
速度分析
速度控制在浇注的各个方面都是至关重要的。高速会引发气体反应、金属碎片过早冻结和进料不一致。这是一个关键步骤,以确保浇口有适当的节流,以尽量减少在浇注过程中的湍流。通常,保持速度低于每秒30英寸是很重要的。阻塞点是铸造工人控制金属速度的方式。该软件包有一个程序,以帮助设计阻塞点时,创建门控系统。
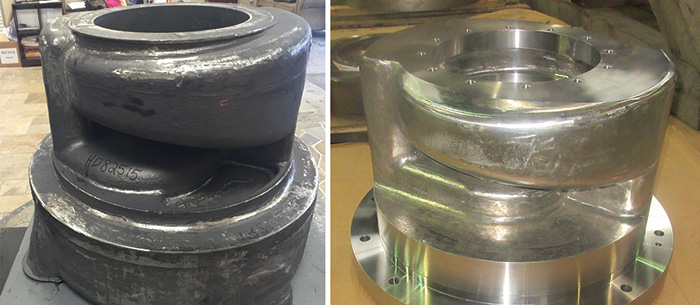
结论
在制造任何工具之前模拟铸造被证明是一个巨大的成功。通过研究最佳和极端条件下的材料密度、温度梯度和速度,项目人员将制造商和最终用户的风险降至最低。制造商能够消除链环的使用,并创造出产生优质结果的混合核心。
完全翻新的元件已经安装完毕,运行时的振动水平比原来的设计大大提高。