BETVICTOR体育官网泵是流体输送操作的核心。意外的失败会破坏生产和利润。工业制造领域的运营商一直在寻找展望未来的方法,在灾难性故障导致生产过程停止之前,知道何时、如何以及为什么需要对泵进行维修。
多年来,制造商一直致力于提高泵的可靠性,并开发了监测泵性能和健康状况的工具。有时候这些工具只会导致“检查引擎灯”的场景。有一个问题,那么下一步是什么?
不断发展的技术使泵和驱动电机可以通过持续的云连接全天候监控。本文阐述了该技术的工作原理,以及该技术如何优化泵的性能、可靠性以及运行和维护成本。
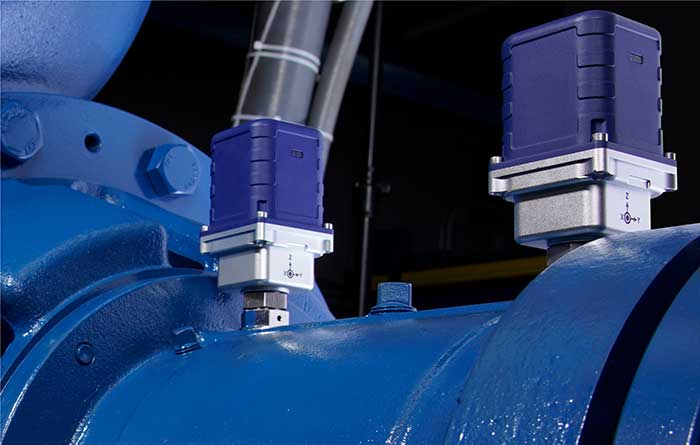
所面临的挑战
在大多数工业生产和加工厂,意外故障可能会对生产计划造成毁灭性的影响,进而影响运营商的底线。泵故障有许多负面影响:
- 中断生产
- 批处理失败
- 过度的停机时间
- 昂贵的修理
- 新零件和运输的成本
- 服务电话费用,包括加班费
- 收入损失或受损
在许多情况下,如果泵的安装和操作正确,就可以防止故障。至少,操作人员应该确保泵是正确对齐的,运行时没有空化,有适当润滑的轴承,足够的底板刚度等。如果这些错误将导致昂贵的——而且是可预防的——维修。
当泵发生故障时,仅更换损坏的部件可能是不够的。对于工厂工作人员来说,找到根本原因也很困难,而且很耗时。
例如,如果机械密封发生故障,如果存在应该解决的轴振动问题,简单地更换它可能无法防止重复故障。找出根本原因可能会导致数小时的假设和试验和错误,以及追踪症状,最终可能需要一定程度的专业知识,而这些专业知识只能由第三方来源提供。
此外,如果泵位于偏远的位置,复杂程度就会增加。在这些装置中,如果没有技术人员在场,就很难对泵进行监控,这也带来了额外的成本和安全问题。
当前行业解决方案
自20世纪90年代以来,工厂一直专注于部署预测性维护(PdM)技术作为提高生产可靠性的解决方案。在泵行业,PdM使用振动和温度监测等技术来观察泵在运行期间的性能和健康状况。早期,PdM是一个手动过程,通过手持设备进行测量,然后记录和分析。这一过程依赖于振动专家来解释数据。
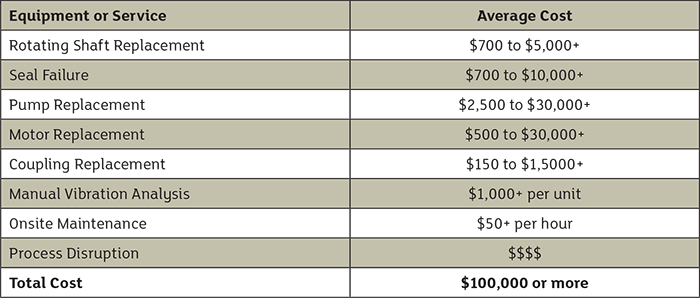
泵行业已经采取措施在PdM中部署先进技术,以实现过程自动化。
虽然目前的一些技术已经实现了数据收集的自动化,但它们仍然存在局限性:
- 完整的机器监控。尽管泵只是机器的一部分,但大多数技术都只是设计来监测泵的。
- 不是真正的远程监控。大多数“远程”监测技术要求技术人员在泵的蓝牙范围内使用移动设备准确地收集数据。
- 没有实时数据。由于远程监控的限制,这消除了实时数据以及24/7监控。
- 报警。其他诊断技术收集的数据只相当于一个没有明确紧急级别的警报。
- 没有维修指导。虽然有一个警告来表示问题,但没有确定根本原因,也没有提供任何修复指导。
- 没有单一来源的数据收集。在一个易于参考和访问的位置收集工厂内所有机器上的数据是很麻烦的。
解决方案
预测监测系统可以识别故障模式,并提供可操作的维修指导,通过Wi-Fi或蜂窝网络接入全天候监测泵和电机。
两个传感器安装在泵上,两个安装在电机上。传感器协同工作,预测泵和电机的健康状况。该功能允许对泵、电机、联轴器和基础的许多性能参数进行诊断性读取和分析,包括:
- 三轴振动读数:设备的振动特征产生有关其健康状况的详细信息,可用于识别即将发生的轴承故障、不对中、空化水平、
管道张力等。 - 温度读数:运行温度升高是即将发生轴承故障、轴承润滑不足和其他问题原因的确切迹象。研究温度趋势可以帮助操作人员检测热故障特征,从而进一步了解可能发生故障的时间。
- 电磁读数:传感器能够监测电机的每分钟真实转数(rpm),并通过电磁工具主动诊断电气故障。
这些数据被收集、编译并传输到云端进行分析,使用工业物联网(IIoT)的全部功能。通过一系列机器学习算法分析数据,可以确定泵和电机的整体健康水平,确定任何警报的根本原因,并生成解决问题的步骤。
当发现潜在问题时,监控系统将通过自动电子邮件报告通知运营商,确定警报级别(是否需要立即处理或需要注意)、根本原因以及可采取的解决方案指导。系统可识别超过20种故障模式。这种破坏模式包括轴承失效、耦合不对中、空化、基础松动等。
场的可靠性
一个系统被安装在一个新的ANSI离心泵上,该泵为一家钢涂层公司使用冷冻水回路。安装完成后,维护团队完成了启动检查表。泵投入使用后,传感器立即发现了两个问题:不对中和基础松动。基础松动的原因确定为基础螺栓松动。维修团队用激光校准工具重新检查了校准,发现确实有问题。
纠正这些问题后,泵开始正常工作。如果没有在早期发现这些问题,泵可能会过早失效。
在正常运行11个月后,出现了新的警报。传感器发现了电机中可能导致电机故障的电气故障。最终用户收到了此故障的警报,并能够在完全故障发生之前更换电机。
结论
新技术利用现有的泵诊断功能,以一种全面的方式查看泵和电机。这些功能有助于优化系统正常运行时间,同时增加设备寿命和操作安全性。
这将减少可能对现场人员和周围环境产生负面影响的事故,同时满足生产计划和配额、效率、维护、维修和更换成本、备件库存和收入优化的苛刻需求。