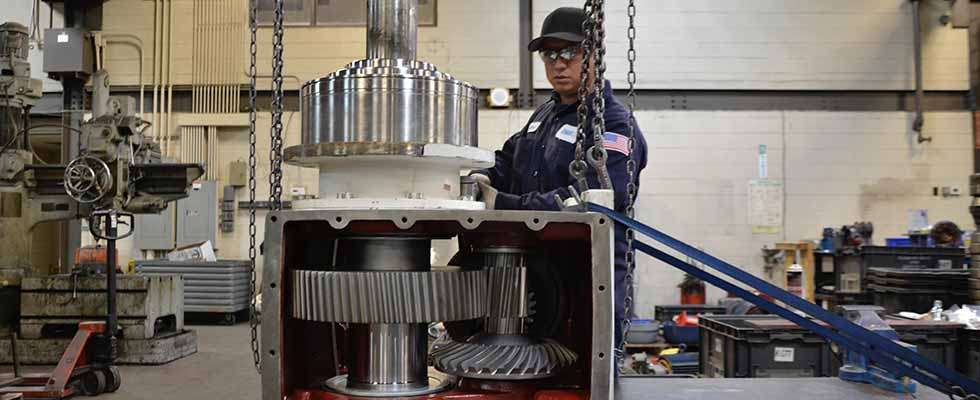
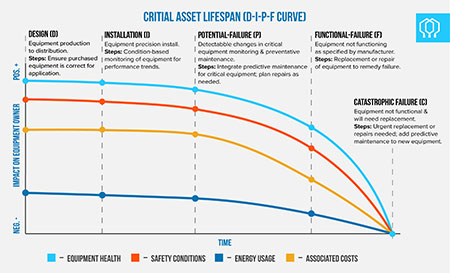
1978年,由F. Stanley Nowlan和Howard F. Heap撰写的以可靠性为中心的维修报告向维修技术人员介绍了潜在故障/功能故障(P-F)曲线的第一次迭代。
该报告由美国国防部发起,是许多不同类型设备可靠性管理的路线图。最初的设计为当前版本的曲线提供了指导,这些版本将继续发展和发展,以保持设备运行时间更长,并将运营成本降至最低。
保持关键设备正常运行的愿望促使我们不断改进曲线,将新的技术与现有的最佳实践结合起来。今天,最普遍接受的版本被称为D-I-P-F曲线,由Doug Plucknette在2006年提出。
设计-“D”
最初版本的曲线中遗漏的内容很可能是设备健康状况最关键的方面之一。选择的电机是否适合应用?电机连接的结构是否正确地确保了将要施加的力?泵是否有足够的头压将液体提升并通过系统的其余部分?
所有这些问题构成了曲线的设计方面。如果设备设计不当,可靠性就会很差,保持设备运行的战斗将使维护技术人员和管理人员都感到沮丧。可靠性的设计阶段将决定可靠性项目的成败,不应被忽视。获得正确的设备规格对设备寿命至关重要。
装置-“我”
任何系统都可能因安装不当而失效。设备的运输会影响设备的可靠性和使用寿命。安装让设计的可靠性扎根。建在沙子上的房子比建在坚实地面上的房子要倒塌许多年。必须应用适当的安装技术来确保系统健康可靠。
安装标准确保系统从一开始就达到设计的可靠性。校准程序必须遵循,包括软脚检查和热生长计算。泵系统中的管道应变也必须消除。
必须进行验收测试,并由可靠性团队成员或系统中合格的维修技术人员验证工作质量。这是用户走向成功之路或失败之沟的时候。
潜在失败-“P”
不管系统设计得多么好,安装得多么完美,失败都会发生。“P”不是设备故障发生的地方,而是故障可以检测到的地方。在“I”和“P”之间的时间是应该引入预测性维护的时间。正是在这段时间内,可以对数据进行趋势分析,以发现潜在的故障点。
%5B3%5D%5B8%5D-980x400.jpg)
定期振动分析、温度监测、油液分析和超声波数据分析等方法可以帮助检测并延长时间,直到出现潜在故障。一旦设备进入潜在故障区域,维修技术人员必须采取纠正措施,并增加监测频率。
纠正措施可以简单地使用超声波数据分析将轴承的润滑恢复到适当的水平,也可以更换磨损的联轴器并验证对齐。
修复在最新振动路径中检测到的安装架裂缝将使用户保持正常运行。这段监测频率增加的时间段还将允许用户趋向故障率并计划维修。在故障的早期阶段进行计划维修几乎总是比等待设备功能故障更便宜。
功能故障(F)
一旦设备进入曲线的功能故障(F)点,它就不再产生其设计的结果。这可能是一个泵失去流量和头部压力或电机将跳闸电流过大。
当设备失去核心功能时,运营、监控和维修成本都会增加。在计划外停机时,维修成本会增加,恢复服务的时间也会缩短。修复设施会评估Rush费用,让用户恢复并运行,这会增加30%到50%的修复成本。
潜在的安全问题,如技术人员受伤,也会随着设备的不稳定而增加。
随着监控的增加,维护技术人员更频繁地靠近设备,增加了受伤的可能性。用户希望避免这种反应阶段,并在进入潜在故障(P)区而不是功能故障(F)区时拉动设备,以保护维护技术人员,并将维修成本降至最低。
灾难性故障(C)
每个人都遇到过这种情况。由于异常,即使采用了最佳的维护实践,也可能发生这种情况。使用基于条件的监视将大大减少这种情况发生的可能性。一旦设备达到这一点,维修成本就会达到最高,维修周期也会达到最长。
通常,这个时候必须决定是修理还是更换。
根据设备的类型,除了高昂的维修成本外,更换设备的可用性也可能是一个因素,以便在合理的时间内恢复生产。对于在设备周围工作的技术人员来说,灾难性故障也是最危险的类型。
通过使用基于状态的监测和预测性维护来避免曲线上的这一点,确保技术人员的安全,降低成本,并将维修时间降至最低。对于关键资产,应将备件或交货期较长的物品放在货架上,或通过维修提供商使用设备存储,以确保设备经过测试并准备安装。这也将确保生产力并将运营成本降至最低。
结论
D-I-P-F曲线是构建可靠的基于条件的可靠性程序的有用工具,例如预测性维护程序。虽然曲线设计改变了,但最终目标没有改变:省钱,继续行驶。
有计划的维修总是比没有计划的维修便宜。通过在曲线的每个部分使用最佳实践,并在故障发生前培养首选供应商列表,用户将拥有健康的设备,并在出现故障时制定计划。